Our Blog
Get inspired by the latest expert insights.
Never miss a new article by subscribing to our newsletter
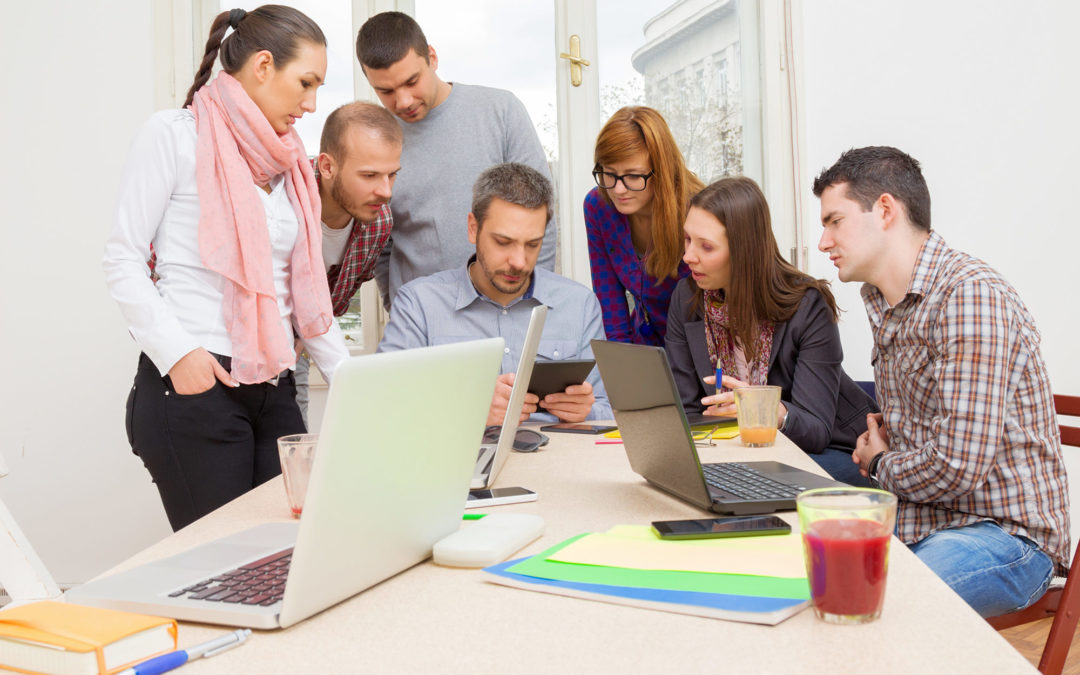
Outstanding Results Require Employee Engagement: The Key to Boosting Ownership and Accountability in the Workplace
Organizations that engage their employees are getting more difficult to find! According...
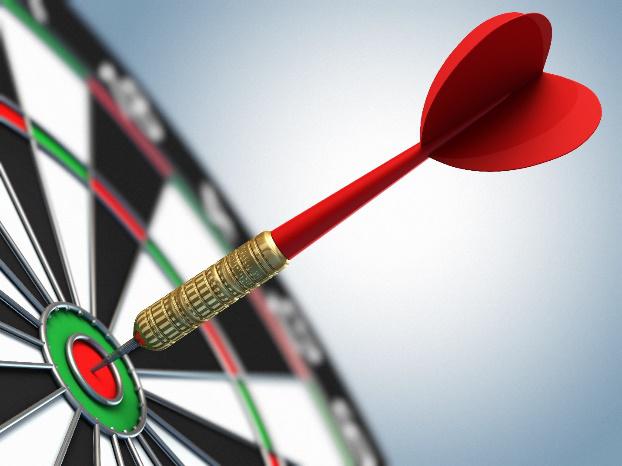
The One Shared Characteristic of All High Performers – Do You Have It?
Seventy-two percent of 516 employers surveyed use management assessments to help make...
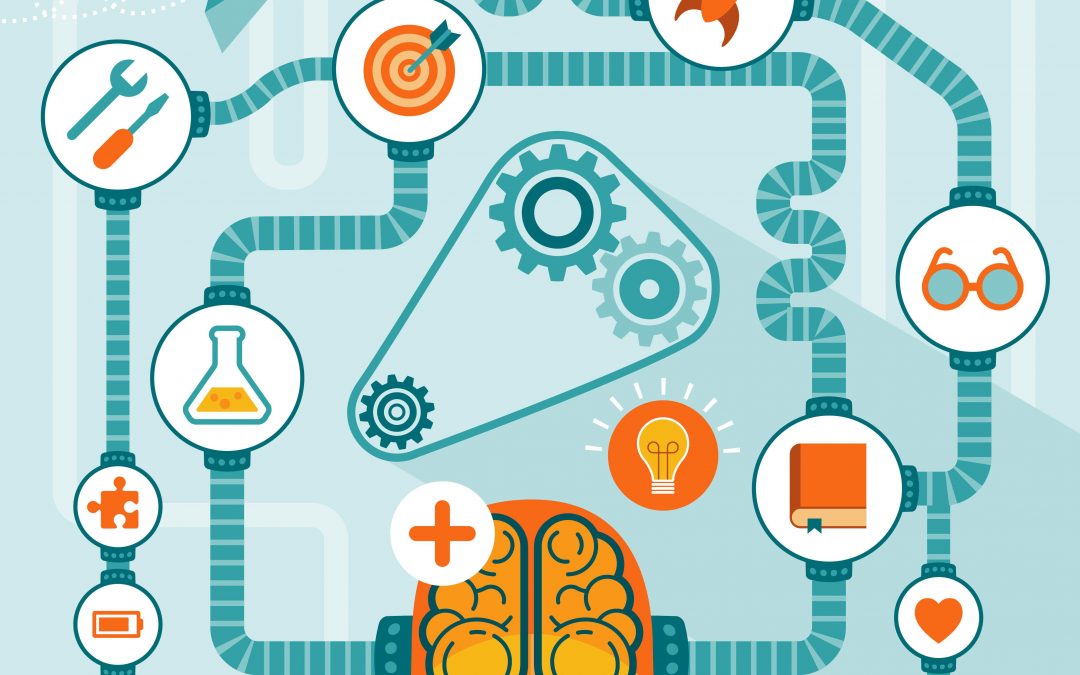
Understanding Lean: Values and Principles
Lean doesn’t mean doing without. It’s a mindset that allows you to continually...
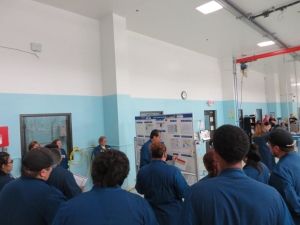
Engaged, Empowered Teams Achieve Their Goals
Imagine if your employees were 100 percent engaged. Imagine a culture where the...
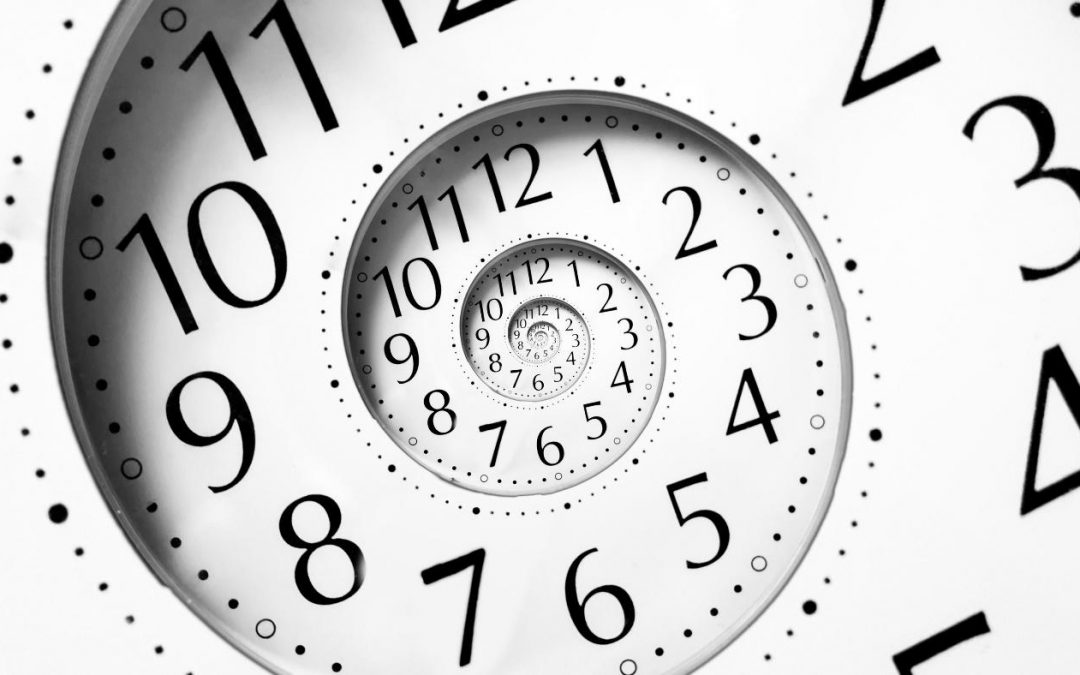
How to Find More Hours in the Day: The Key to Productivity
“Time is what we want most and use worst.” – William Penn. We all have the same 24...
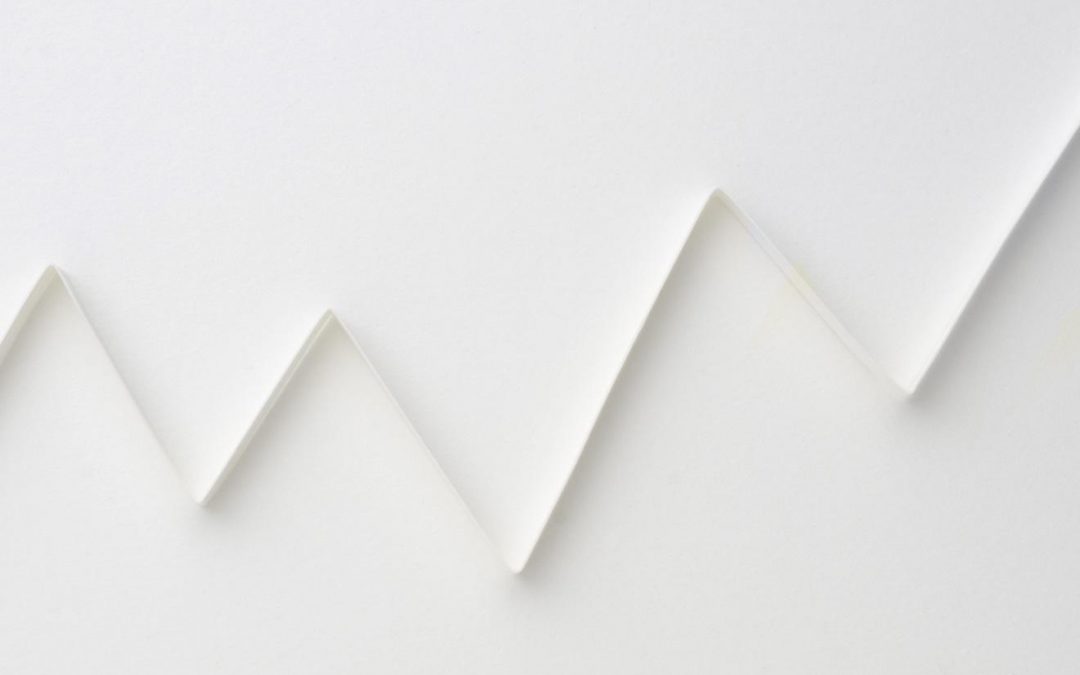
Why You’re not Meeting Your Organizational Goals (And How to Start)
We set personal goals every year, but a month passes (or mere days for some of us) and...
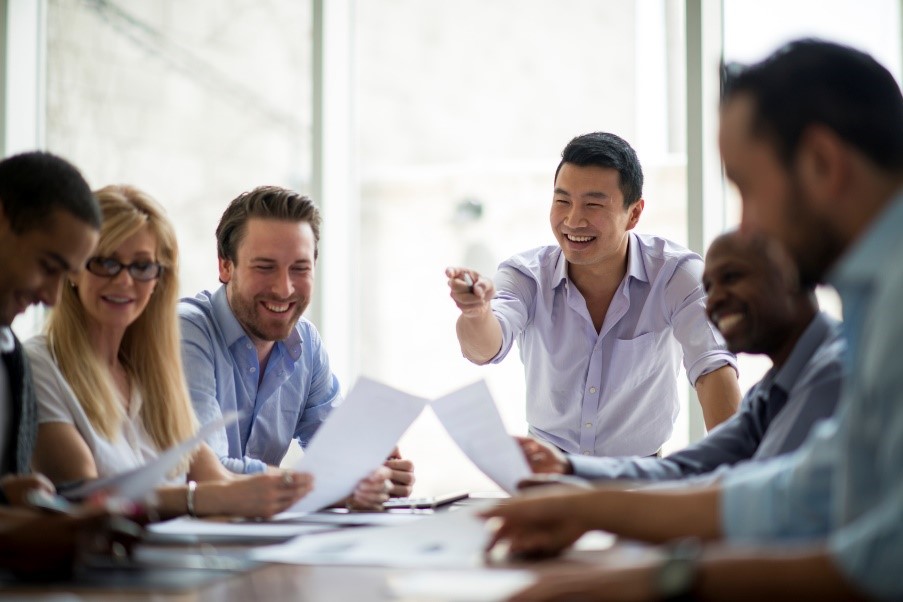
High-Performance Work Teams Aren’t Just Problem Solvers
Problem solving with Lean, Six Sigma, and Kaizen doesn’t automatically create high-...
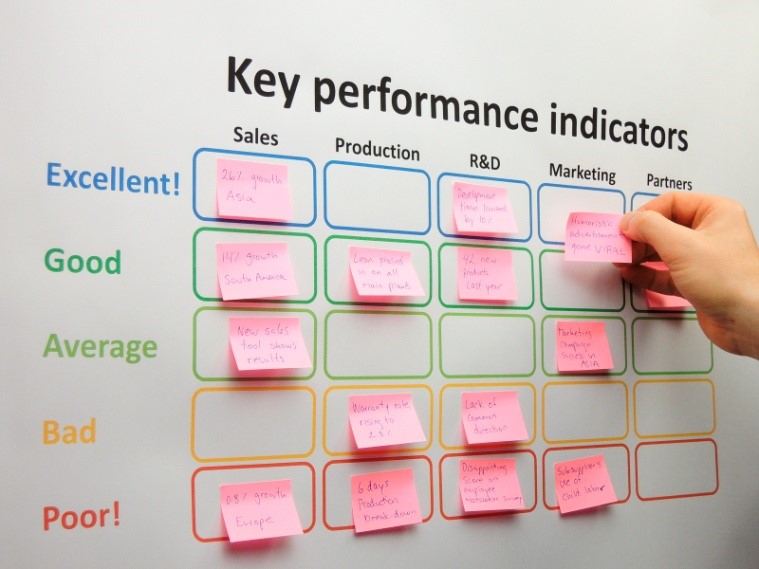
Performance Measurements Aren’t Good or Bad, They’re Tools for Improvement
Life isn’t black and white, and neither is workplace success. Too often,...
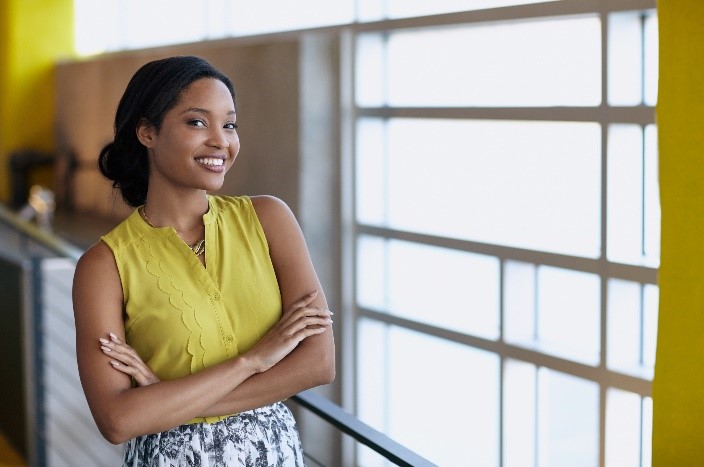
Leadership: Getting Work Accomplished Through Others
Leadership: Getting Work Accomplished Through Others Are you setting your team up for...
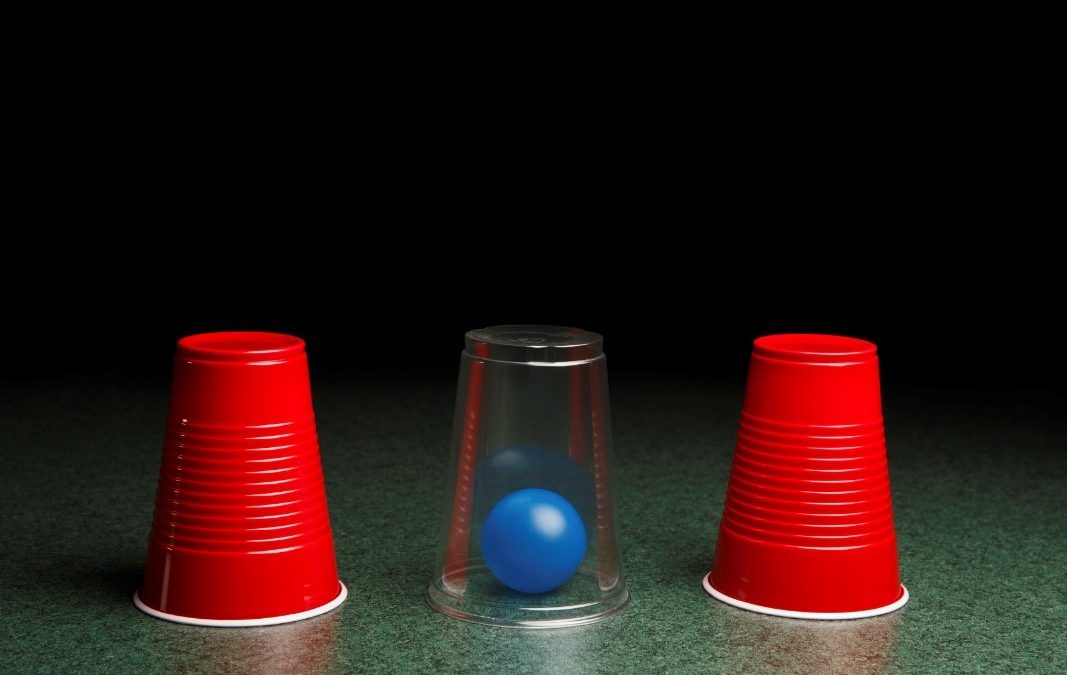
Voice of the Customer: There’s No Guesswork in Customer Satisfaction
Don’t ever assume: Especially when it comes to what your customers want. Business...
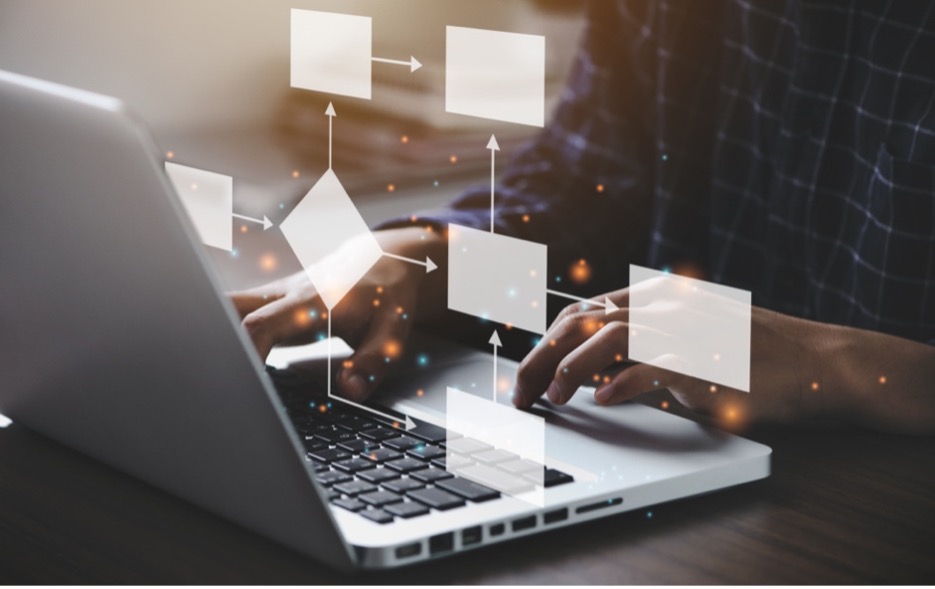
Is Your Company’s Productivity Stagnant or Declining? How to use Audits to Encourage Sustainability and Prevent Atrophy
It’s not uncommon for teams that have achieved a high level of performance to begin to...
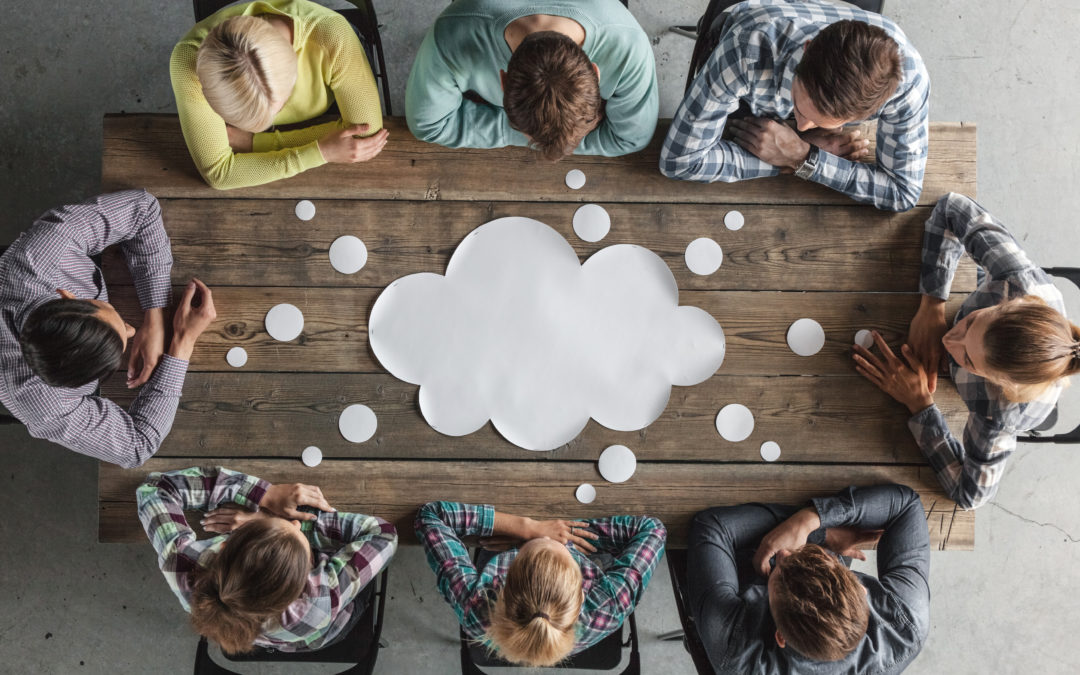
How Communication Infrastructure Elevates Performance
When communication stops, performance atrophies. When communication is constant,...
The Dorsey Group empowers clients to overcome challenges, unlock potential, and achieve long-term success in today's competitive business landscape.
Choose The Dorsey Group as your partner for turnaround management consultancy. Hire our experienced turnaround consultants to help you assess your business's internal problems, and come up with the most logical solutions to get your business going.